Welding Methods
The term welding of plastics refers to the indissoluble bonding of thermoplastics using heat and pressure with or without the use of an additional material. This term does not cover the processes ambiguously described as cold or swelling welding. All welding methods take place when the material at the gap and surface zone is in the plastic state. The thread-like molecules of the pressed together parts combine and intertwine to form a homogeneous union. Basically only plastics of the same type, e. g. PP with PP can be welded together and within this provision only those with the same or similar (neighbouring) molecular weight and same density, different colours however do not have an effect.
BUTT WELDING
Before butt welding, the two surfaces to be welded are heated to welding temperature by a heating plate. It is then removed and the two plasticized surfaces are pressed together to form a weld.
SOCKET WELDING
In heated tool socket welding, pipe and fittings are welded with an overlap. A heating tool (or tools) with socket and plug-shaped faces is used to heat the two pieces to be welded; they are then brought together and fused. The pipe end, heating tool, and fitting socket are matched so that fusion pressure is built up during fusion. When the pipe diameter is: > 63 mm for PE 80, PE 100, and PP > 50 mm for PVDF a suitable welding equipment should be used.
EXTRUSION WELDING
Extrusion welding is used, amongst other things, for connecting thick walled parts. Welding is carried out with a welding filler. The extrusion welding equipment consists of a small extruder. The extruded material is pressed down by a welding shoe. As with high heat stability can be used as materials for the shoe, PTFE has been the most successful. The welding shoe must be suited to the shape of the individual seam.
Extrusion welding is similar to hot gas welding. In comparison with hot gas welding shorter working times and higher mechanical strength properties are achieved with high seam quality and low internal stresses
ELECTROFUSION WELDING
The surfaces to be welded, i. e. the pipe outer surface and the socket inside surface, are heated to welding temperature and fused by electric current, through the resistance of wires within the socket.
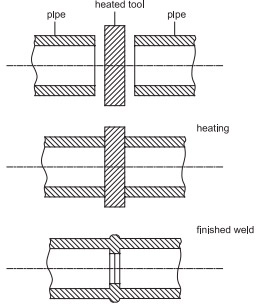
WELDING FAULTS
- Sheets and wire have not been heated equally
- Temperature and air volume are not correct
- Sheet and wire are not clean enough
- The air is not water, oil and dust free
- Air has been trapped within the welding seam area
- The volume of the welding wire is insufficient to prevent notches in the welding seam area
- Incorrect arrangement of the sheets
- Welded too quickly so the welding wire remained round and was not sufficiently shaped resulting in no or incomplete bonding.
- Thermal damage has been caused as a result of using too high a welding temperature